VPR Energy is part of VITOL, a globally operating energy trader. VITOL’s origin lies mainly in the trade of oil, but also in products derived from oil, such as petrol, diesel, naphtha etc. Gradually the range of products expanded. Additionally, storage tanks were added to the portfolio through a large share in VTTI. In 2017, VPR Energy was added as a fully-owned refinery, producing 110,000 barrels per day. VITOL is also a shareholder in a number of other refineries in Europe. However, VPR belongs entirely to VITOL, making it a unique asset in the VITOL organisation. It is a relatively horizontal organisation and has grown to 50 employees since 2017. These employees are divided between office personnel, including planning, engineering, HSE and H&R, and operators, who help keep the factory running 24/7.
Sander Albertsma
Today, we are speaking to Sander Albertsma, EH&S manager at VPR and responsible for Environment, Health and Safety.
Sander started working for Koch in 2011, the owner of the refinery at the time. My background was a consultant for DHV and my expertise related particularly to technical safety. Due to developments in the laws and regulations, this was expanded to include issues relating to the environment, amongst other things. These became increasingly important. We are talking about, for example, changes to permits, nitrogen deposition, CO2 emissions, energy efficiency, and the emission of substances of very high concern (SVHC) related to hydrocarbon. All these aspects meant my role was diverse but also increasingly important and challenging. In 2017, we were acquired by VITOL and substantial investments were made.
In 2019, a process change for the furnace was implemented to ensure optimal heat recovery. Now, in 2022, we have just restarted operations after making further improvements to our energy efficiency. Heat recovery is now even more efficient thanks to a different type of heat exchanger. We are making the necessary changes to shrink our footprint.
VPR Energy’s ambition is to “be the greenest”
When this facility was built in 1994, the splitter – or condensate splitter, as it was called at the time – was still part of the Van Ommeren Terminal. Their vision was that, in a hub such as Rotterdam, the terminal could be used in the process of storing and loading natural-gas condensate, for example. But by building a splitter, you could also produce intermediate products. Through the years, you can see how the whole thing turned into the refinery we have today: an instrument to serve the market. By working closely with VITOL trading, we are able to respond to the demands in the market on behalf of our parent company. For example, naphtha or Jet 1 (jet fuel). We strive to do this as safely and reliably as possible. We also aim to be the refinery with the smallest environmental footprint. Our goal is to achieve lower CO2 emissions than set down in the Emission Trading Scheme benchmark. Another step we have taken with the conversions we made this year is a decrease in NOx emissions and a reduction in nitrogen deposition, currently a problem in the Netherlands.
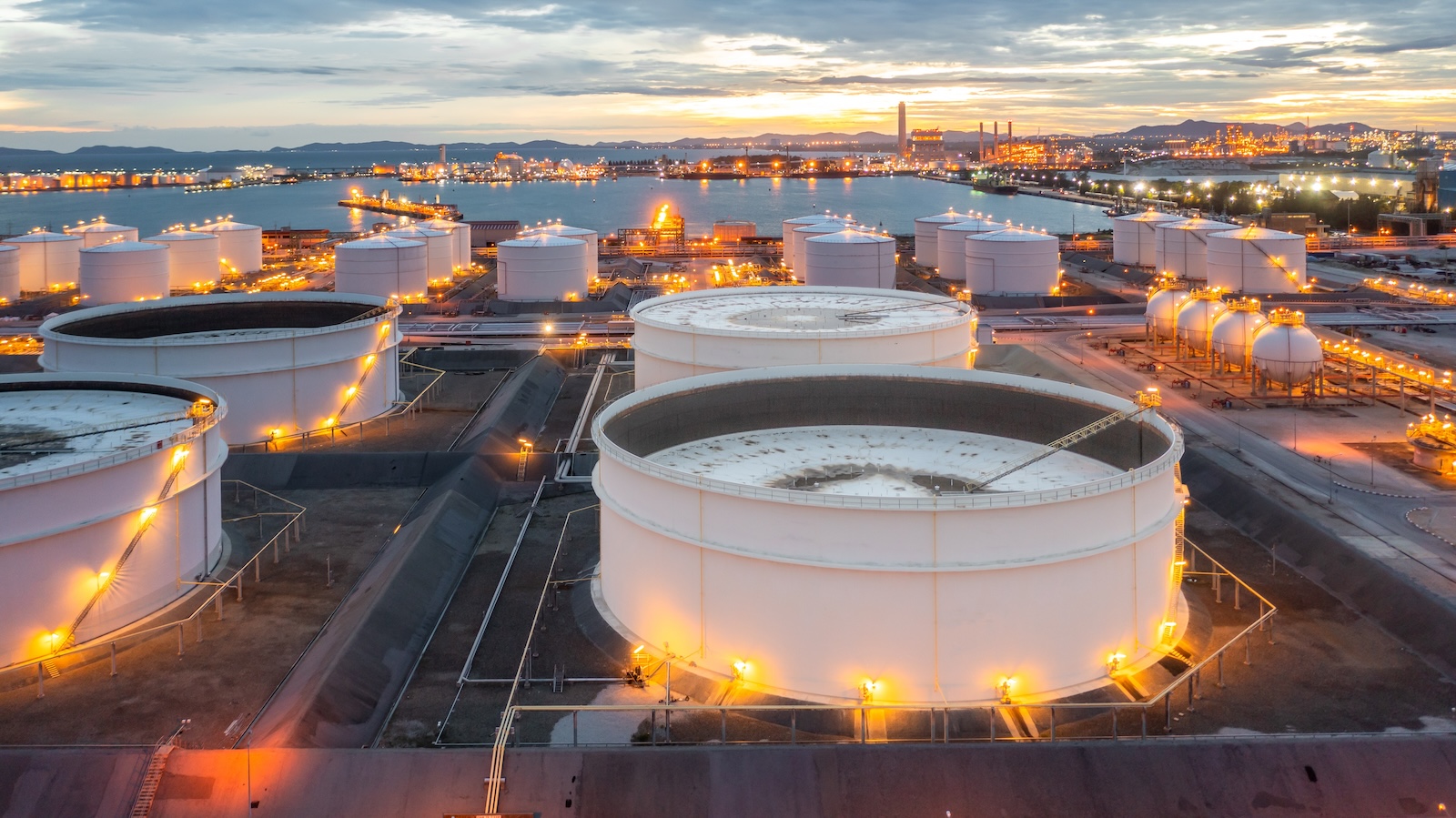
Our ambition is to be the “greenest refinery”. If you look at our emissions profile, a large part is made up of emissions to air: CO2, NOx, nitrogen oxides, but also sulfur dioxide. Our emissions are moving to the lower end of the BREF range, the reference value for the best available techniques. For example, we have managed to halve our NOx emissions. So we certainly have green ambitions.
This also applies to our emissions to water, which make up a smaller percentage than emissions to air, where we are also working to reduce our emission profile. Research is currently being done into reusing our water effluent. The idea is that by using reverse osmosis, we can make the water even cleaner so that we can reuse it in our own processes. This would also reduce our use of clean drinking water – an excellent development.
Collaboration with TP Europe
Following a recommendation from our neighbours, VOPAK, we contacted TP Europe in 2019.
At the time, we were still carrying out random checks to monitor our emissions and noting the results in an Excel overview. Despite doing our best, we were aware that we were missing some information to be able to calculate our annual emissions. The competent authorities were also becoming more critical regarding the monitoring and following up of repairs to leaks in the whole installation. We needed objective research and a database of all possible leak points in the installation. We also needed a method of providing accurate insight into what components are present in our emissions. For example, what percentage of our emission profile concerns SVHC? We just did not have enough information to show this. So I started asking neighbouring companies and consultants. Who would be a good partner for VPR? The name TP Europe was mentioned surprisingly frequently, and this led to our initial collaboration, which has only increased to this day. The real eye-opener for us was mapping our monitoring points again and setting up a source database. Naturally, this requires investing a lot of time, but the result is that we have created the best monitoring and management system for our emissions.
Maintenance
In an effort to further manage our emissions, our Safety Manager, Remco Hasenack, together with our maintenance department, has developed a plan to address all the leaks that were found in the near future. This will, of course, require a certain amount of raising awareness and he has worked with them to create the right workflow to carry out this process quickly and thoroughly. Especially in terms of an explanation to the men in the field of what the driving incentive was for VPR to do this. The environmental aspect is crucial here, of course. You want to prevent the emission of hydrocarbons into the air as much as possible. The exposure of outside personnel to these emissions has also been included in this plan, as has the economic loss of the product.
Additional research
As of this year, in addition to the Leak Detection and Repair project, we have also been carrying out research such as Optical Gas Imaging (OGI) and Ultrasound valve and flare research.
If we can compare the aspects of environment, safety and economic loss to these results, then we will have even more extensive control.
The flare research, in particular, which falls under the competent authorities, produced results you would not normally be able to discover by yourself. Product loss is an important subject in terms of energy efficiency. But we are also trying to produce our product range using as little regular energy as possible. Naturally, there is a demand throughout VITOL for alternative fuels or other sources of energy, such as wind energy, for example.
Tips to colleagues in the market
We have been taking part in various external consultation structures with other Dutch refineries, for example, VEMOBIN, a consultation structure that includes companies that all produce fuel or energy for the transport sector.
What VPR would strongly recommend to colleagues in the market is to implement the changes we did to the furnace. Why? Well, nitrogen deposition can be a serious bottleneck in the Netherlands, and this is a very good step to a significant reduction.